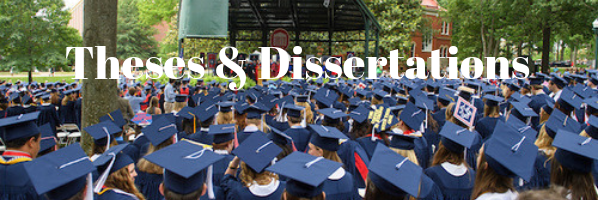
Date of Award
1-1-2015
Document Type
Thesis
Degree Name
M.S. in Engineering Science
Department
Mechanical Engineering
First Advisor
Jeffrey A. Roux
Second Advisor
Jagdish P. Sharma
Third Advisor
Tejas Pandya
Relational Format
dissertation/thesis
Abstract
Pultrusion is a continuous process for manufacturing composite materials with constant cross section. Reinforced fibers are pulled through a resin, possibly folloby a separate injection chamber preforming system, and into a heated die, where the resin undergoes complete wetout. Thus the required pultruded composite is obtained in the desired profile. The main objective of this research is to present a numerical model employing the finite volume technique to simulate the resin flow in a tapered injection chamber through the fiber reinforcement when compaction of the fiber reinforcement is taken into account. The numerical model predicts the impact of design and process parameters on wetout, resin pressure field, resin velocity field, and compaction of the fiber reinforcement. This work predicts the impact of tapering the walls of the injection chamber on the minimum injection pressure necessary to achieve complete wetout. Even a small tapering of the injection chamber walls causes a significant impact on the minimum injection pressure required to achieve complete wetout. The compaction phenomenon which changes with any of these parameters is also considered in this work, which gives a more realistic modeling of the complete pultrusion process. In this study, the processing parameters were varied for a particular set of geometric parameters and the wetout criteria were discussed at various conditions. Finally an efficient compaction model is defined with a tapered geometry injection chamber and preferred working parameters.
Recommended Citation
Masuram, Naveen Babu, "Fiber compaction and wetout in tapered resin injection pultrusion manufacturing" (2015). Electronic Theses and Dissertations. 1301.
https://egrove.olemiss.edu/etd/1301