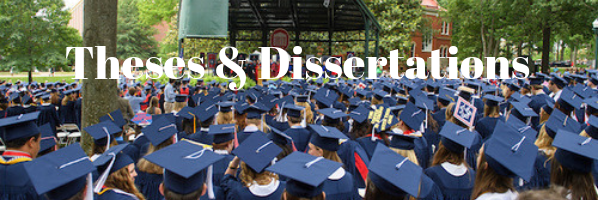
Date of Award
1-1-2016
Document Type
Dissertation
Degree Name
Ph.D. in Pharmaceutical Sciences
Department
Biomolecular Sciences
First Advisor
Michael A. Repka
Second Advisor
Samir A. Ross
Third Advisor
Seongbong Jo
Relational Format
dissertation/thesis
Abstract
Hot-melt extrusion (HME) is a promising technology for the production of new chemical entities in the developmental pipeline and for improving products already on the market. The first objective of this research work was to describe a continuous process for the production of solid lipid nanoparticles (SLN) as drug-carrier systems via hot-melt extrusion (HME) using Quality by Design (QbD) principles. Fenofibrate SLN were prepared by combining two processes: HME technology for melt-emulsification and high-pressure homogenization (HPH) for size reduction. Varying the process parameters enabled the production of SLN below 200 nm. At the end of a 5-h in-vitro dissolution study, a SLN formulation released 92– 93% of drug, whereas drug release was approximately 65% and 45% for the marketed micronized formulation and crude drug, respectively. The second objective of this research work was to develop pH-independent/dependent sustained release (SR) tablets of ondansetron HCl dihydrate (OND). The in-vitro release study demonstrated sustained release for 24 h with 90% of drug release in formulations using stearic acid in combination with ethyl cellulose, whereas 100% drug release in 8 h for stearic acid-hydroxypropylcellulose matrices. The third objective of this research work was apply a QbD approach based on design of experiments as a risk-based proactive approach to achieve predictable critical quality attributes (CQAs) to develop a dry-granulation process for controlled release formulation of OND SR tablets by twin-screw extruder. The effect of screw speed, feed rate and amount of fumaric acid on the particle size and flow properties of the granules and time required for complete and controlled release of the drug from the dosage was optimized by 23 factorial design. Based on the design of experiment (DOE) results, a formulation comprising of 2.5 % (w/w) fumaric acid extruded at high screw speed (100 rpm) and low feed rate (1%) was found to fulfill requisites of an optimum formulation. The fourth objective was to understand the dehydration behavior of OND during HME process. Hydrates of active pharmaceutical ingredients may undergo dehydration during the manufacturing process and/or storage. This can affect the physiochemical properties of the formulation including solubility, dissolution rate, bioavailability and stability.
Recommended Citation
Patil, Hemlata, "Hot-melt extrusion: A versatile pharmaceutical technology" (2016). Electronic Theses and Dissertations. 1493.
https://egrove.olemiss.edu/etd/1493