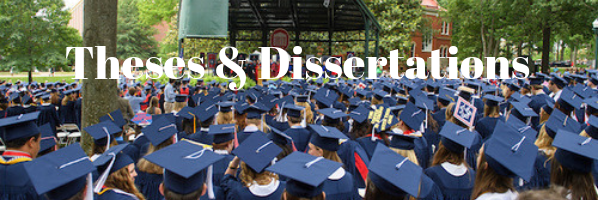
Date of Award
1-1-2022
Document Type
Thesis
Degree Name
M.S. in Engineering Science
Department
Engineering Science
First Advisor
Shan Jiang
Second Advisor
Arunachalam Rajendran
Third Advisor
Shan Jiang
Relational Format
dissertation/thesis
Abstract
Accurate computational modeling of the ballistic response of heterogenous materials is crucial when designing lightweight armor and protective structures. Currently, due to the structural complexity inherent in composites, this behavior is poorly understood. In the present work, a novel computational model to describe the glass fiber-reinforced polymer (GRP) response to shock and impact loadings was implemented in the commercially available Abaqus© finite element software via a VUMAT subroutine. Before damage initiation, the model utilized an experimentally-determined tetragonally-symmetric stiffness matrix for the elastic representation of the GRP. Once damage was initiated, a hyperelastic continuum damage mechanics (CDM) based model described the GRP behavior. The shock and impact simulations utilized plate-on-plate impact and projectile penetration tests respectively. Calibration of the computational model involved simulation of a plate-impact experiment available in open literature, whereby a thick steel or aluminum flyer plate impacted a thin GRP plate at velocities ranging from 111.69 m/s to 417.96 m/s. User-defined computational model parameters were calibrated to realistically match the experimental particle velocity profiles. To validate the calibrated model, Abaqus simulations of fragment-simulating projectile (FSP) penetration into 44 mm thick GRP targets at velocities ranging from 246 m/s to 800 m/s were performed. A sensitivity study was performed to investigate the influence of fiber and matrix damage parameters on depth-of-penetration (DOP). The computational results underestimated the DOP and the GRP back surface displacement while showing good agreement with peak compressive shock stresses at different through-thickness depths compared to experimental values. Furthermore, matrix and fiber damage propagation and concentrations throughout the GRP were investigated, revealing profound GRP degradation occurred approximately 50 μs after the initial impact. A wider lateral region of matrix and fiber failure was observed closer to the GRP impact and rear surfaces, and fiber damage was observed to be primarily caused by compressive failures.
Recommended Citation
Fraser, James Stuart, "Abaqus Implementation of a Hyperelastic Damage Model for Glass-Reinforced Polymers under Shock and Impact Loading" (2022). Electronic Theses and Dissertations. 2217.
https://egrove.olemiss.edu/etd/2217
Concentration/Emphasis
Mechanical Engineering