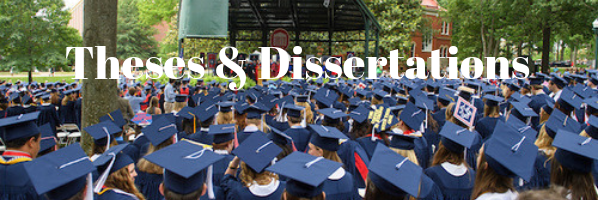
Date of Award
8-1-2022
Document Type
Thesis
Degree Name
M.S. in Engineering Science
First Advisor
Farhad Farzbod
Second Advisor
Yiwei Han
Third Advisor
Shan Jiang
School
University of Mississippi
Relational Format
dissertation/thesis
Abstract
The traditional approach to casting non-operative arm fractures involves fully covering a large portion of the forearm, often including a portion of the palm. The use of gypsum plaster and plaster materials often results in cutaneous problems or in more severe cases swelling, pressure sores, or deep vein thrombosis. Other disadvantages include the weight, time it takes to harden, or the damage in contact with water. The objective of the project is to create a durable but breathable custom-made design for an arm brace that will replace the traditional solutions by overcoming their disadvantages. Several research groups and companies provide alternative solutions; however, this study presents a novel approach to the utilization of topology optimization, specifically the density-based method. The development of a prototype can be broken into several stages. The process starts with a scanning procedure using a handheld scanner, and the creation of a generic solid brace. The next step is a simulation study in COMSOL involving topology optimization and density method to optimize the material distribution to reduce weight and create holes in the design to provide ventilation while satisfying set constraints to ensure structural support to immobilize the affected area. Minor modifications to the design such as splitting the model into two halves and creating connectors follow after simulation before the model is 3D printed. Several prototypes were printed on Stereolithography (SLA) and Fused Deposition Method (FDM) printers and tested for mechanical properties and energy absorption in comparison to traditional fiber-glass casts. The data obtained using an instrumented weight impact test tower was used to compare and evaluate the material and performance of the additively manufactured and traditional fiber-glass prototypes. The 3D-printed PLA sample prototype absorbed more energy during the impact compared to the fiberglass sample, which would provide a more suitable solution in case of an impact on the cast; however, the material used in this prototype, polylactic acid (PLA) filament, was very brittle. Therefore, the next generation of the prototype was printed using acrylonitrile butadiene styrene (ABS-M30TM) filament to observe whether such material would improve the functionality and performance in future testing.
Recommended Citation
Janatova, Tereza, "Design and Fabrication of Additively Manufactured Arm Cast Using Topology Optimization" (2022). Electronic Theses and Dissertations. 2378.
https://egrove.olemiss.edu/etd/2378