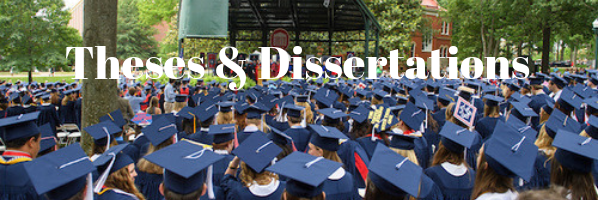
Date of Award
1-1-2023
Document Type
Thesis
Degree Name
M.S. in Pharmaceutical Science
First Advisor
Micheal A. Repka
Second Advisor
Dr. Walter Chambliss
Third Advisor
Seongbong Jo
School
University of Mississippi
Relational Format
dissertation/thesis
Abstract
Mefenamic acid, a non-steroidal anti-inflammatory drug generally used for the treatment of pain, has poor solubility (0.2 mg/ml of water at 250C) and limited bio-availability. Thus, to improve these various techniques are used such as micronization, solvent evaporation, hot melt extrusion, chemical modification, pH adjustment, solid dispersion formation, complexation, co-solvency, micellar solubilization, hydrotropic, ultra-rapid freezing process, etc. Thus, to improve the improve the solubility Solvent Evaporation technique was employed to obtain the solid dispersion of Mefenamic acid and Eudragit® RL-PO followed by Hot Melt Extrusion to obtain the extrudates. The extrusion of Mefenamic acid (MA) and Eudragit® RL-PO was done using a 11mm twin screw co-rotating extruder (Process 11® Thermo Scientific, Pittsburgh, PA, USA) and screw speed of 50 rpm with a standard screw configuration; an extrusion temperature was maintained in the range of 140oC - 200oC was employed for extrusion with 1.75 mm die. The physical and chemical characteristics of the extrudates were evaluated using various analytical techniques.
The Differential Scanning Calorimetry (DSC) thermograms showed that the melting temperature of the Mefenamic acid (MA) decreased with increasing drug loading. The endothermic peak of pure MA was observed at 231.4°C, which shifted to lower temperature ranges of 225.2°C, 217.4°C, 207.6°C, and 200.2°C for drug loading of 16%, 20%, 25%, and 30%, respectively. These results indicate that the extrudates were amorphous in nature and the drug was molecularly dispersed within the polymer matrix.
The Fourier Transform Infrared (FTIR) spectra of the extrudates showed no new chemical bonds or interactions between the drug and polymer. This suggests that the drug and polymer remained physically mixed and did not undergo any chemical changes during the extrusion process.
In vitro dissolution studies showed that the extrudates had significantly improved dissolution rates compared to pure MA. The dissolution rate was found to increase with increasing drug loading. The extrudates with a drug loading of 30% showed a dissolution rate of 88.3% in 30 minutes, while pure MA exhibited only 27.5% dissolution in the same period.
Recommended Citation
Thawani, Lokesh Mukesh, "Formulation & Evaluation of In-Vitro Mefenamic Acid Oral Disintegrating Tablets Using Solvent Evaporation and HME" (2023). Electronic Theses and Dissertations. 2589.
https://egrove.olemiss.edu/etd/2589