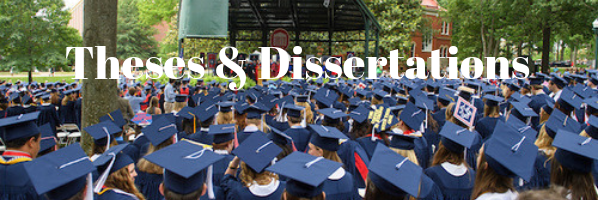
Date of Award
1-1-2023
Document Type
Dissertation
Degree Name
Ph.D. in Pharmaceutical Sciences
First Advisor
Micheal Repka
Second Advisor
Eman Ashour
Third Advisor
Eman Ashour
School
University of Mississippi
Relational Format
dissertation/thesis
Abstract
Fused Deposition Modeling (FDM) three-dimensional (3D) printing is the most studied method compared to other 3D printing technologies. However, the optimization of the 3D printing design must be done throughout the process for crucial parameters to deliver the desired dose. Optimizing the drug content and tablet weight has challenged researchers while designing the 3D printing dosage form. In this study, the concept of reference tablet and the mathematical modeling were used to correlate the volume of the printed object with its weight to control the height, diameter, and percentage infill of the 3D printed tablets to adjust the dose without the need to know the feedstock density. To test the applicability of this method, polylactic acid (PLA) filament was used to print cylindrical tablets in the line and grid patterns in three different percentages infill, 100, 70, and 40%. The tablets were printed with or without a wall and with two different wall widths. The same experiment was repeated using four 3D printer models. The results showed that when the mathematical modeling was applied to multiple case studies, the 3D printed tablets` weight and drug content were within the targeted range, proving that the tablet dose, volume, and percentage infill can be monitored and controlled. A software was coded using Patheon to develop a computerized version of the mathematical modeling. The results showed that when using the software on multiple case studies, the 3D printed tablets` weight was within the targeted range, proving the applicability of the software.
The software was used to optimize the weight of FDM 3D printed floating tablets. The designs of Carbamazepine floating tablets were studied using Gyroid and Quarter Cubic printing patterns in 70 % and 50 % infill. The extrusion temperature (120-140°C), extrusion speed (75-100 RPM), the printing temperature was maintained at 178°C, and the printing speed at 20 mm/sec. Under the specified processing parameters, the successful extrusion and printing of a polymeric matrix containing Ethylcellulose, Polyethylene glycol, and Soluplus® with 25% drug loading occurred. The printed tablets had a floating time of 12-24 hours, with a complete CBZ release within 21-32 hours.
Recommended Citation
Omari, Sundus, "Mathematical and Computerized Modeling to Optimize the Dimensions and Percentage Infill for the Targeted Dose of Different 3D Printed Pharmaceutical Designs with Multiple Case Studies" (2023). Electronic Theses and Dissertations. 2704.
https://egrove.olemiss.edu/etd/2704